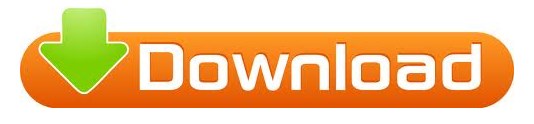

Masao Kubota, Haguruma Nyumon, Tokyo : Ohmsha, Ltd., 1963. This article is reproduced with the permission. Click Here to Select Bevel Gears Spiral and Straight Bevel Gears for machine designers Secondary operations can be given except for the teeth. Gears that have been hardened and ground that has grade-0 accuracy, strength, abrasion resistance and quietness. For example in the case of materials, S45C of machine structural carbon steel, SCM415 of machine structual alloy steel and MC901 of engineering plastic, etc.

Incidentally, all gears manufactured by KHK use the Gleason method.įurthermore, there are also variations in gears in terms of teeth pitch (modules, etc.), whether polished or not, and materials used.
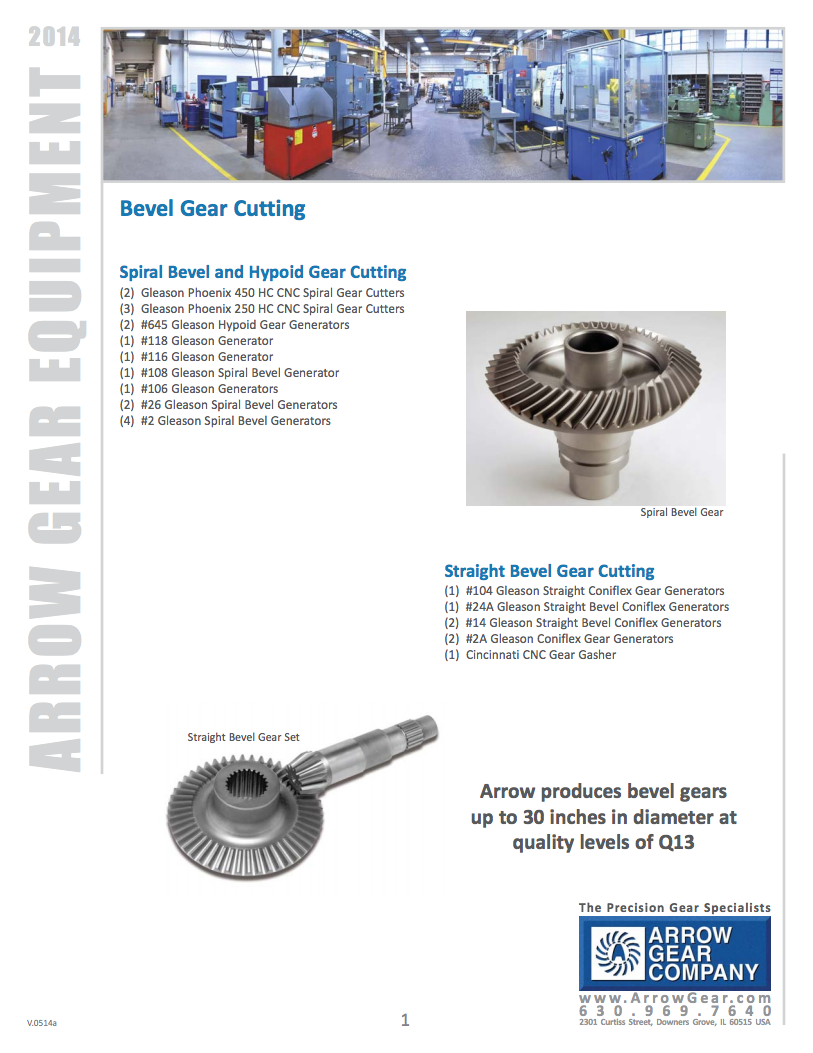
However, because of the fact that manufacture facilities for straight bevel gears are becoming rare and the fact that straight bevel gears teeth cannot be polished, making spiral bevel gears which can be polished superior in terms of noise reduction, spiral bevel gears are likely to become more common in the future.īevel gears can be generally classified by their manufacturing methods, namely the Gleason method and Klingelnberg method, which each have differing teeth shapes, and presently most gears use the Gleason method. Looking at bevel gears from the differences in helix angles, they can be generally classified into straight bevel gears, which do not have helix angles, and spiral bevel gears (including zerol bevel gears), which do have helix angles. The standard definition of a Bevel Gear is a cone-shaped gear which transmits power between 2 intersecting axels.
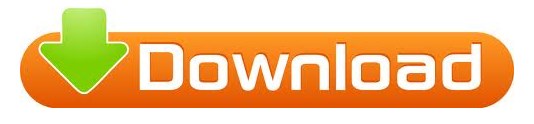